Introduction to Hanger Shot Blasting Technology
Hanger shot blasting machines represent a revolutionary advancement in industrial surface preparation technology. These automated systems utilize a continuous conveyor mechanism to transport workpieces through a high-intensity blasting chamber, where metallic abrasives are propelled at high velocity to clean, descale, deburr, and prepare surfaces for subsequent finishing processes. Unlike traditional manual blasting methods, hanger-type machines offer unparalleled consistency, efficiency, and throughput capacity.
Key Productivity Advantages
- Continuous Operation Capability
The hanging conveyor system allows for non-stop processing of parts, significantly reducing downtime between batches. A typical hanger machine can process 300-500 hooks per hour depending on configuration. - Automated Surface Treatment
Programmable logic controllers (PLCs) ensure precise control over blasting parameters including:- Abrasive flow rate (typically 120-180 kg/min)
- Wheel rotational speed (1800-3600 RPM)
- Conveyor speed (0.5-3 m/min adjustable)
- Labor Efficiency
Reduces manual labor requirements by up to 70% compared to manual blasting, with one operator capable of managing multiple machines simultaneously. - Energy Optimization
Modern systems feature regenerative abrasive recovery systems that recycle 85-92% of media, coupled with energy-efficient 15-75 kW turbine blast wheels.
Technical Specifications for Maximum Output
- Workpiece Capacity: Handles parts up to 2m in length and 500kg in weight
- Surface Coverage: Achieves 95-98% coverage in single pass
- Dust Collection: Integrated systems with 99.7% filtration efficiency
- Surface Profile: Creates optimal 50-100 micron anchor patterns for coating adhesion
Industry Applications
Particularly effective for:
- Automotive components (axles, gears, brake parts)
- Foundry castings (iron, steel, aluminum)
- Structural steel (I-beams, plates)
- Aerospace components (landing gear, turbine parts)
Maintenance Considerations for Sustained Productivity
- Daily inspection of wear parts (liners, blades, elevators)
- Monthly lubrication of conveyor chains
- Quarterly abrasive sieve analysis
- Annual motor and electrical system checks
The ROI period for hanger shot blasting machines typically ranges from 12-24 months based on production volume, with most users reporting 40-60% increases in surface treatment throughput.
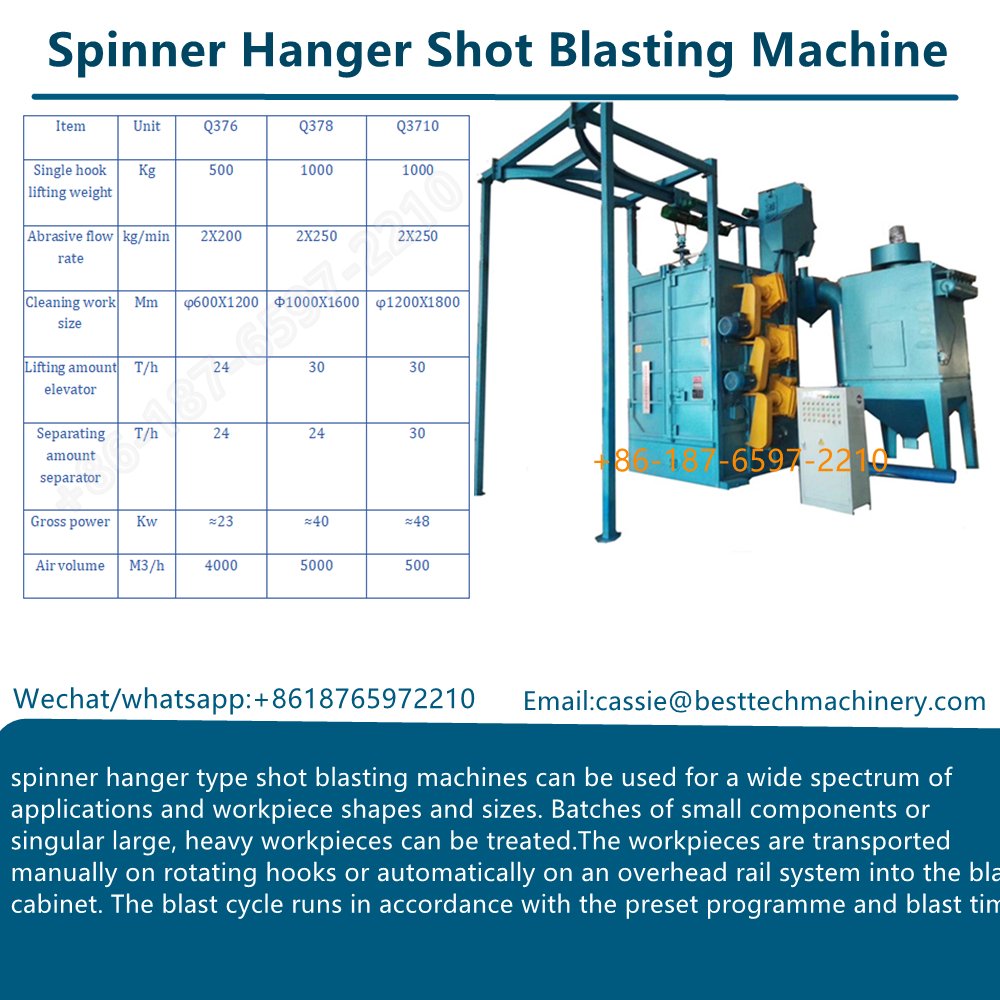
How Hanger Shot Blasting Machines Revolutionize Industrial Productivity
1. Continuous Processing Capability
Unlike batch processing systems, hanger shot blasting machines feature continuous conveyor systems that allow:
- Non-stop operation with typical throughput of 300-500 hooks/hour
- 24/7 operation potential with minimal downtime
- Automated loading/unloading stations reducing human intervention
2. Optimized Surface Treatment Parameters
Precision-controlled systems ensure maximum efficiency through:
- Programmable abrasive flow rates (120-180 kg/min standard)
- Adjustable conveyor speeds (0.5-3 m/min)
- Multiple turbine configurations (15-75 kW wheels)
- Automated media recycling (85-92% recovery rates)
3. Labor Efficiency Improvements
The automation features reduce labor requirements by:
- 70% reduction in operators compared to manual blasting
- One technician can monitor multiple machines
- Eliminates physically demanding manual blasting work
4. Quality Consistency Benefits
Automated systems deliver:
- 95-98% consistent surface coverage
- Repeatable surface profiles (50-100 micron)
- Reduced rework rates (typically <2%)
5. Maintenance Advantages
Productivity is maintained through:
- Quick-change wear parts (liners, blades)
- Automated lubrication systems
- Predictive maintenance monitoring
- Average uptime of 92-95%
6. Energy and Cost Savings
Modern systems provide:
- 30-40% energy savings vs older models
- Reduced abrasive consumption
- Lower waste disposal costs
- ROI typically 12-24 months
Implementation Considerations
To maximize productivity gains:
- Proper workpiece hanging configuration
- Optimal abrasive selection
- Regular equipment calibration
- Operator training programs
Leading manufacturers report 40-60% productivity increases after implementing hanger shot blasting systems, making them essential for competitive surface treatment operations.
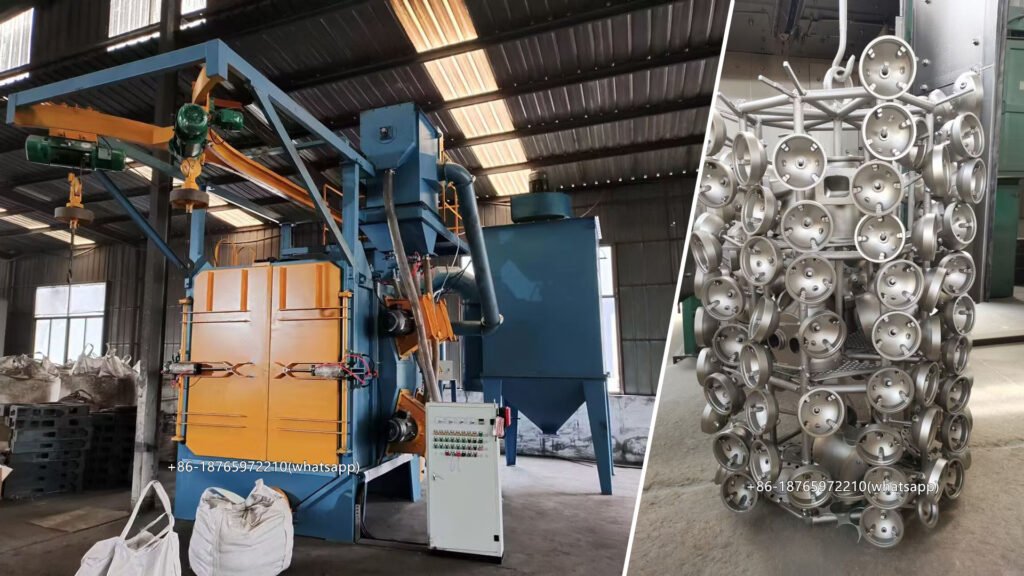
Choosing the Right Hanger Shot Blasting Machine: A Technical Buyer’s Guide
Optimize Surface Preparation Efficiency Through Strategic Equipment Selection
Selecting the proper hanger shot blasting system is critical for maximizing ROI in industrial surface treatment. This guide examines key decision factors to match equipment capabilities with your production requirements.
Core Selection Criteria
- Workpiece Specifications
- Max dimensions (L x W x H)
- Weight range per hook (kg/lbs)
- Material composition (steel, aluminum, cast iron)
- Geometry complexity (internal cavities, fragile features)
- Production Requirements
Parameter | Standard Range | Calculation Formula |
---|---|---|
Hourly Throughput | 150-800 hooks/hr | (Cycle time + load/unload)⁻¹ |
Annual Capacity | 100K-500K parts/yr | Hooks/hr × Shift hrs × Days |
Shift Configuration | 1-3 shifts | Capital cost ÷ Savings/shift |
- Surface Quality Standards
- Required cleanliness level (SA 2.5 to SA 3)
- Anchor profile depth (μm/mil)
- Surface coverage uniformity (>95% typical)
Technical Configuration Options
A. Blast Wheel System
- 2-8 turbine configuration
- Wheel power: 15-75 kW each
- Adjustable RPM (1800-3600)
B. Conveyor System
- Chain speed: 0.5-4 m/min
- Loading height: 800-1200 mm
- Hook spacing: 600-2000 mm
C. Media Recovery System
- Magnetic separator efficiency (≥98%)
- Airwash separator capacity (kg/hr)
- Media consumption/recovery ratio
Facility Integration Factors
- Footprint Analysis
- Machine length: 8-25 meters
- Clearance requirements: 1m perimeter
- Loading/unloading zone space
- Utility Connections
- Power: 50-400 kVA (3-phase)
- Air supply: 6-10 bar @ 10-30 m³/min
- Dust collector exhaust: 5000-20,000 m³/hr
Compliance & Safety Features
- CE/OSHA noise compliance (<85 dB)
- Explosion-proof ratings (for Al/Mg alloys)
- Emergency stop systems (category 4 PL e)
- Dust emission controls (<5 mg/m³)
Vendor Evaluation Checklist
- Field service response time (<48 hrs)
- Wear part availability (blades, liners)
- Control system compatibility (Industry 4.0)
- Test run capabilities (bring sample parts)
Smart Selection Tips
- Future-Proofing
- Select 20-30% above current capacity
- Ensure upgrade path for automation
- Abrasive Flexibility
- Configure for steel grit/shot, ceramic, or specialty media
- Digital Integration
- Demand OPC-UA connectivity
- Require remote monitoring capability
Selecting the right hanger shot blasting system typically yields:
- 30-50% reduction in processing cost/part
- 90%+ equipment utilization rates
- ROI within 18-36 months
Partner with manufacturers offering application engineering support to conduct thorough process validation before finalizing your investment.
This guide provides actionable technical criteria for evaluating hanger shot blasting systems. Always request material testing with your actual components to verify performance claims before procurement. The optimal machine balances current requirements with future operational flexibility.
Hanger Shot Blasting Machine – FAQ
1. What is a hanger shot blasting machine?
A hanger shot blasting machine is a type of blast cleaning equipment where components are suspended from a rotating hook or hanger. It is designed for surface cleaning, descaling, deburring, and surface preparation of medium to large parts, especially those with complex geometries.
2. What materials can be processed with a hanger shot blasting machine?
Common materials include:
- Cast iron
- Steel
- Aluminum
- Forged parts
- Heat-treated components
3. What industries use hanger shot blasting machines?
Hanger type machines are widely used in:
- Foundries
- Automotive manufacturing
- Metal fabrication
- Aerospace
- Railways
- Heavy machinery
4. What are the advantages of a hanger shot blasting machine?
- Handles delicate or complex parts without part-on-part contact
- Suitable for heavy and irregular-shaped workpieces
- High blasting efficiency
- Compact footprint with integrated dust collection options
- Minimal part handling, often automated loading/unloading
5. What sizes and weights of workpieces can it handle?
Depending on the machine model, hanger shot blasting machines can process components weighing from a few kilograms up to several tons. The size range typically depends on the diameter and height of the blasting chamber and the lifting capacity of the hook system.
6. Are hanger shot blasting machines automated?
Yes. Modern hanger machines can be fully or semi-automated. They often include features like:
- Programmable logic controllers (PLC)
- Touchscreen HMIs
- Automated hook rotation
- Automatic door opening/closing
- Shot flow regulation
7. What are the types of hanger shot blasting machines?
There are typically two main types:
- Monorail Type: Continuous or semi-continuous blasting with overhead rail system.
- Batch Type: Rotating hooks for batch processing of workpieces.
8. How is the shot media collected and reused?
After blasting, the spent shot and debris fall into a collection hopper. The shot is then:
- Transported by a screw or belt conveyor
- Cleaned by an air separator
- Recycled back into the blasting system
Dust and fines are collected by an integrated dust collector.
9. How do I choose the right hanger shot blasting machine?
Consider the following factors:
- Size, shape, and weight of your parts
- Required blasting intensity
- Desired production rate
- Available floor space
- Type of abrasive to be used
10. What maintenance is required?
Routine maintenance includes:
- Checking and replacing worn blast wheel components
- Cleaning or replacing filters in the dust collector
- Inspecting hangers and rotating mechanisms
- Monitoring abrasive levels and quality