In the world of industrial manufacturing, surface preparation is a critical step that significantly impacts product quality, durability, and performance. Shot blast machinery plays a vital role in this process by removing surface contaminants, improving adhesion for coatings, and enhancing overall surface properties. With the increasing demand for precision and efficiency, modern shot blast equipment offers advanced solutions tailored to a wide range of applications and industries.
What is Shot Blasting?
Shot blasting is a mechanical cleaning process where abrasive media (usually steel shots or grits) are propelled at high speed onto the surface of a material. The impact removes rust, scale, paint, sand, and other unwanted materials from the surface, leaving a clean, roughened texture ideal for further processing, such as painting, welding, or coating.
Types of Shot Blast Machinery
There are various types of shot blasting machines, each designed for specific workpieces and production needs:
- Tumble Belt Shot Blasting Machine: Ideal for small to medium-sized batch parts, especially castings and forgings. The tumbling action ensures even cleaning of all surfaces.
- Spinner Hanger Shot Blasting Machine: Used for delicate or complex-shaped components. Workpieces are suspended and blasted while rotating to avoid damage and ensure complete coverage.
- Roller Conveyor Shot Blasting Machine: Perfect for large and flat materials like steel plates, beams, and structural components.
- Table Type Shot Blasting Machine: Best for large, heavy workpieces that cannot be tumbled.
- Hanger Through Shot Blasting Machine: Suitable for continuous blasting of larger components on a conveyor system.
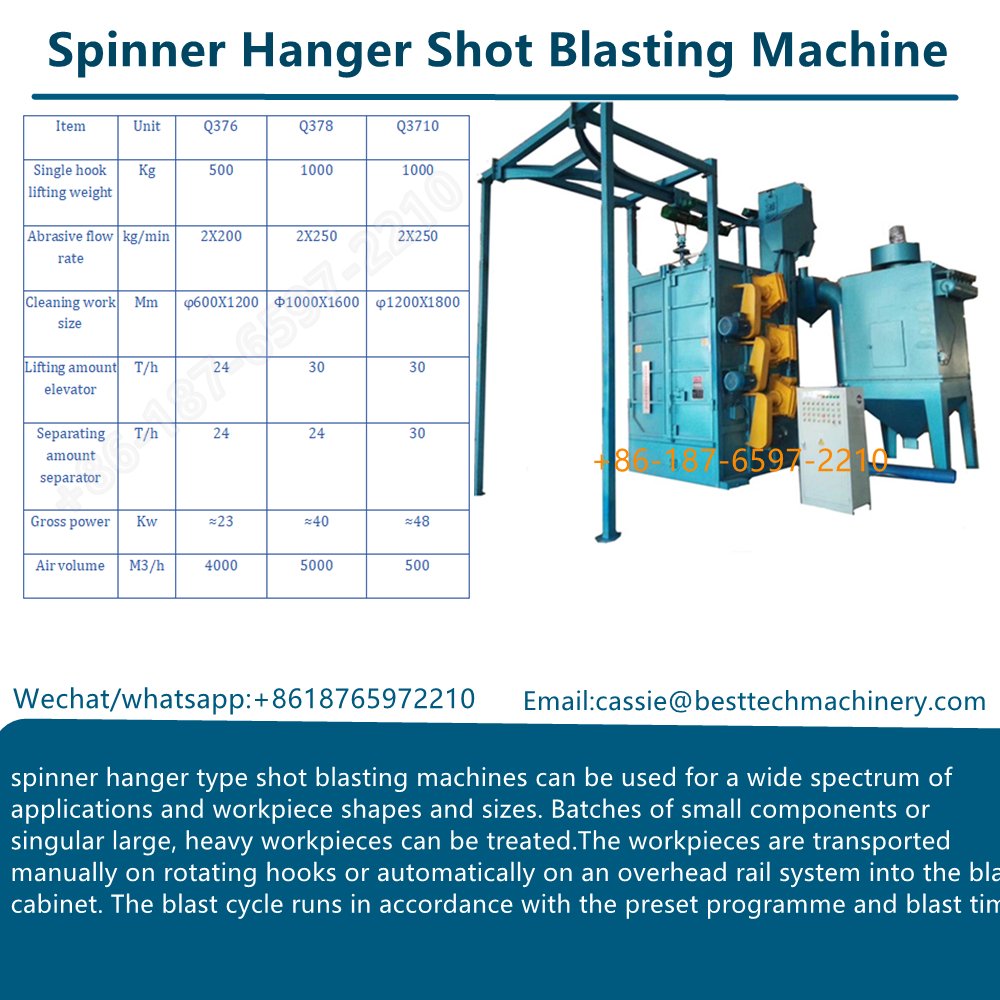
Core Shot Blast Machinery Components
Modern shot blast machines are sophisticated systems. Key components include:
- Blast Wheel(s): The heart of centrifugal blast machines. High-speed turbines propel abrasive media via centrifugal force. Key elements are the impeller (rotating blades) and control cage (directs media flow). Wheel size and power dictate capacity and intensity.
- Blast Cabinet/Enclosure: Contains the blasting process, protecting the operator and environment. Includes viewing windows, lighting, and access doors. Can range from small cabinets for individual parts to large rooms or specialized chambers for structural steel or pipes.
- Media Recycling System (Reclaimer): Essential for efficiency and cost control. Typically involves:
- Elevator: Moves used media from the floor/bottom of the cabinet.
- Separator: Cleans the media by removing dust, fines, and contaminant particles (usually via air wash or magnetic separation). Vital for maintaining blasting efficiency and surface cleanliness.
- Media Storage Hopper: Holds cleaned media ready for reuse.
- Dust Collector: Removes fine dust and particulate generated during blasting, ensuring operator safety (respirable silica risks), maintaining visibility, and protecting the environment. Critical for compliance with health and safety regulations.
- Material Handling System: Transports the workpiece through the blasting zone. Options include:
- Tumble Blast: Rotating barrels for small, bulk parts.
- Table Blast: Rotary tables for batch processing.
- Hanger Blast: Overhead conveyors for large or complex parts (e.g., forgings, castings).
- Belt Blast: Continuous belt systems for flat sheets or plates.
- Roller Conveyor: For structural steel beams, pipes, etc.
- Control System: PLC-based controls for regulating blast wheel speed, conveyor speed, media feed rate, dust collector operation, and monitoring system health.
The Shot Blast Media: Choosing the Right Tool
The choice of media dramatically impacts results:
- Metallic Media:
- Steel Grit: Angular, cuts aggressively. Excellent for fast rust/mill scale removal and creating a sharp anchor profile.
- Steel Shot: Round, peens surfaces. Ideal for cleaning without excessive profile, peening, and finishing.
- Cut Wire: Chopped steel wire, offers a mix of grit/sharpness and shot/roundness properties.
- Stainless Steel Shot/Grit: Used where contamination prevention is critical (e.g., food processing, medical).
- Non-Metallic Media:
- Aluminum Oxide: Very hard, angular. Used for high-precision cleaning, etching, and creating aggressive profiles. Reusable.
- Silicon Carbide: Extremely hard, sharp. Fast cutting for tough contaminants but brittle. Often used for specialized applications.
- Glass Bead: Round, creates a smooth, satin finish without significantly altering dimensions. Good for cleaning and cosmetic finishing.
- Plastic Media: Gentle, used on softer substrates (aluminum, composites, plastics) or for paint stripping without damaging underlying material.
- Agricultural Media (Walnut Shells, Corn Cob): Gentle abrasives for delicate cleaning or polishing.
Benefits of Shot Blast Machinery
- Consistent Surface Quality: Automated shot blasting ensures uniform surface finish and repeatable results.
- Improved Coating Adhesion: Proper surface preparation enhances paint, powder, and other coatings’ bond strength.
- Increased Productivity: High-speed blasting processes reduce manual labor and time spent on surface cleaning.
- Cost Efficiency: Less rework, reduced material waste, and longer-lasting coatings contribute to lower production costs.
- Environmental Safety: Enclosed systems with dust collection features help maintain a clean and safe working environment.
Surface Preparation Solutions Across Industries
Shot blasting is used across a variety of industries including:
- Foundry and Forging: Cleaning castings, removing sand, and preparing surfaces for inspection or coating.
- Automotive: Removing scale from engine components, axles, and gears.
- Construction and Infrastructure: Preparing steel structures, bridges, and pipes for painting or galvanizing.
- Shipbuilding and Marine: Descaling large hulls and removing corrosion from marine components.
- Aerospace: Prepping high-precision parts without damaging critical tolerances.
Key Parameters for Effective Shot Blasting
Surface Profile (Anchor Pattern): Measured in microns or mils, defined by the media and parameters. Must match coating specifications.
Media Selection: Type, size, shape, hardness.
Blast Pressure/Impeller Speed: Controls velocity and impact energy.
Media Flow Rate: Determines intensity and coverage.
Distance: From nozzle/wheel to surface.
Angle of Impact: Optimal angle depends on goal (cleaning vs. profiling).
Exposure Time: How long the surface is blasted.
Working with an experienced shot blasting equipment manufacturer ensures you receive a customized solution tailored to your specific needs, along with support in installation, training, and maintenance.
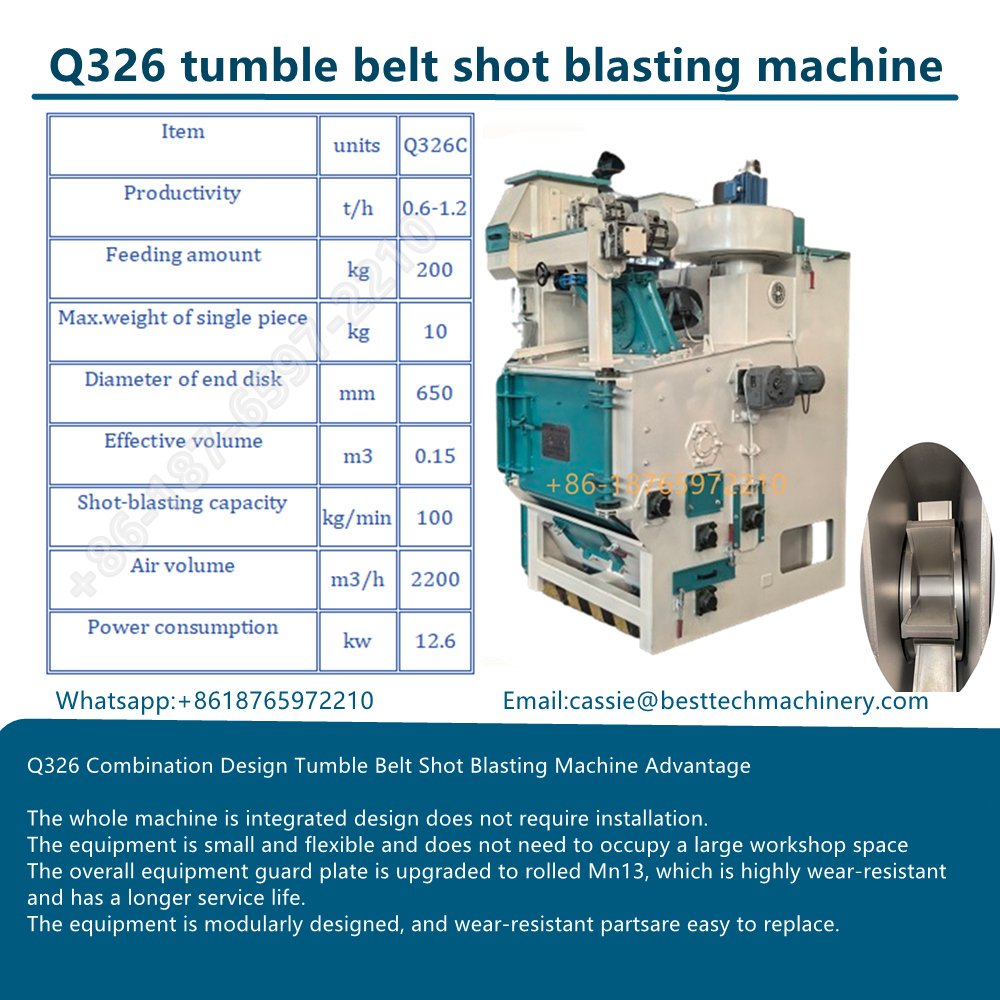
Why Choose Shot Blasting Machine for Metal Surface Preparation?
In metalworking industries, surface preparation is a crucial step before painting, coating, welding, or further fabrication. Among various surface treatment methods, shot blasting machines have become the preferred solution for preparing metal surfaces due to their efficiency, versatility, and superior results. This article explores the key reasons why shot blasting is the ideal choice for metal surface preparation.
1. Effective Removal of Contaminants
Metal surfaces often accumulate rust, scale, old paint, welding slag, or sand residues that must be removed before further processing. Shot blasting efficiently eliminates these contaminants using high-speed abrasive media, ensuring the base metal is clean and ready for finishing. Unlike manual or chemical methods, it offers thorough and uniform cleaning without leaving residue.
2. Improved Surface Adhesion
One of the main purposes of surface preparation is to improve the adhesion of coatings, paints, or other treatments. Shot blasting creates a uniform, roughened surface profile (also called anchor pattern), which enhances the mechanical bonding of coatings. This results in better durability, corrosion resistance, and overall performance of the final product.
3. Increased Productivity and Efficiency
Shot blasting machines are automated and highly efficient. They can clean large volumes of parts in a short time with minimal manual intervention. Whether it’s batch processing or continuous inline blasting, these machines reduce labor costs, save time, and increase overall production throughput.
4. Consistent and Repeatable Results
Compared to manual cleaning or grinding, shot blasting provides consistent surface quality across all parts. The blasting intensity, media type, and exposure time can be precisely controlled to ensure uniform results, which is especially important in industries with strict quality standards such as aerospace, automotive, and construction.
5. Versatility for Different Metal Components
Shot blasting machines are available in various configurations—such as tumble belt, spinner hanger, roller conveyor, and table type—to accommodate different shapes, sizes, and weights of metal parts. Whether you are cleaning small castings, heavy steel plates, or complex welded assemblies, there is a machine designed to meet your needs.
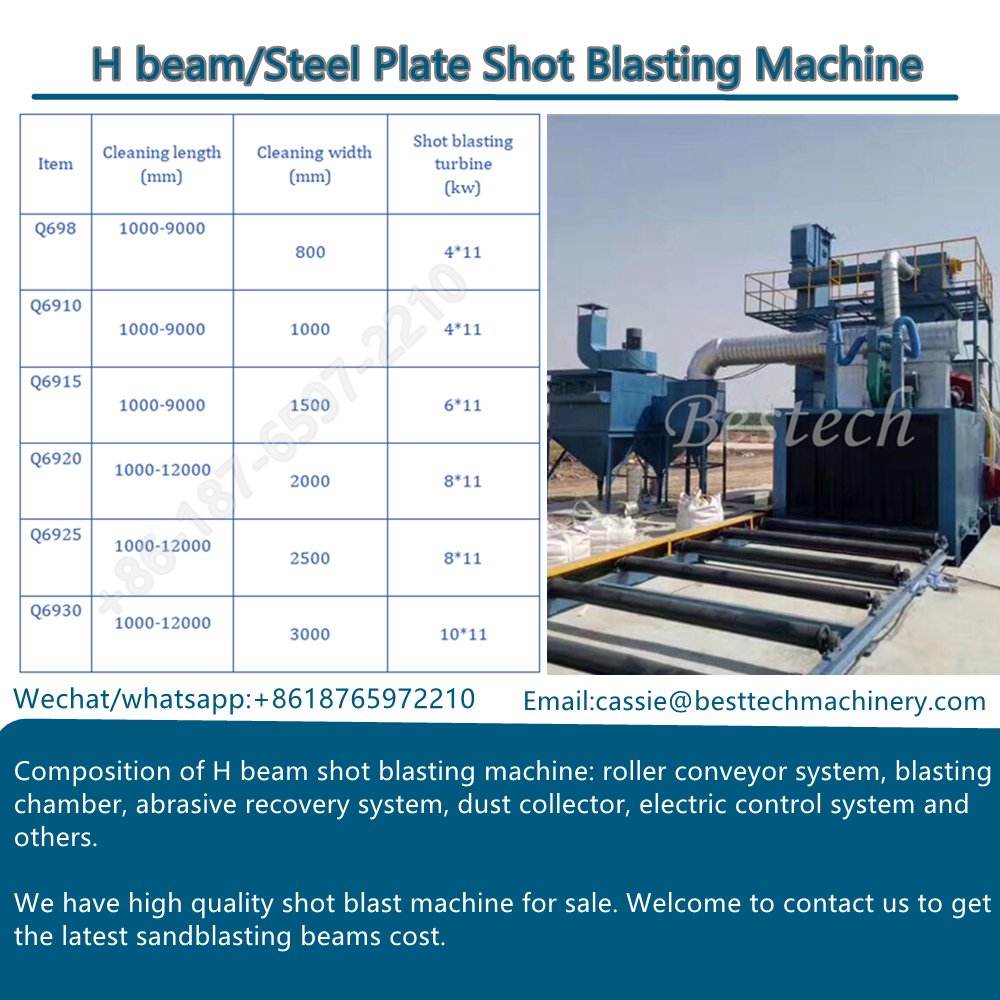
6. Environmentally Friendly and Safe
Modern shot blasting systems are enclosed and equipped with dust collectors, which minimize air pollution and improve workplace safety. Unlike chemical cleaning, shot blasting does not use hazardous solvents or produce toxic waste, making it an eco-friendly alternative for surface treatment.
7. Enhanced Component Lifespan and Performance
By removing stress points, scale, and micro-cracks, shot blasting can actually improve the fatigue strength and service life of metal parts. In applications like aerospace and heavy machinery, this added durability is a critical advantage.
Shot blasting machines are an indispensable tool for preparing metal surfaces in a wide range of industries. They offer fast, consistent, and environmentally responsible cleaning while enhancing coating adhesion and part performance. Whether you’re working in foundry, fabrication, construction, or automotive sectors, choosing a shot blasting machine ensures your metal surfaces meet the highest quality standards—every time.
Choosing the Right Solution
Selecting the optimal shot blast machine requires careful consideration:
- Workpiece: Size, shape, weight, material, fragility, volume/batch size.
- Surface Condition: Type and thickness of contaminant/coating removal required.
- Required Finish: Desired cleanliness standard (e.g., ISO 8501-1 Sa 2.5, Sa 3), anchor profile depth (micron/mil), and surface texture.
- Production Rate: Throughput requirements (parts/hour, tons/hour).
- Automation Needs: Manual, semi-automated, fully automated (robotic).
- Space & Utility Constraints: Available footprint, power, air supply.
- Environmental & Safety Regulations: Dust control, noise reduction requirements.
Conclusion
Shot blast machinery is a cornerstone of efficient and reliable surface preparation in modern manufacturing. With a wide variety of machines and technologies available, industries can achieve high-quality finishes, extend the life of their products, and improve overall production efficiency. Investing in the right surface preparation solutions is not just about cleaning—it’s about setting the foundation for excellence in every finished product.