Industrial metal surfaces need serious treatment to stay in top shape. That’s where hanger shot blasting machines come in. These workhorses remove rust, clean surfaces, and prepare metal parts for coatings, making them a staple in automotive, aerospace, and manufacturing industries.
Unlike other blasting systems, hanger shot blasters suspend workpieces on rotating hooks, ensuring full exposure to the abrasive media. This results in a cleaner, more uniform finish—without the hassle of tumbling delicate or complex parts.
Introduction to Hanger Shot Blasting Technology
Hanger shot blasting machines are industrial surface treatment systems designed for batch processing of components suspended from overhead conveyors. These robust machines utilize centrifugal wheel blast technology to remove scale, rust, and contaminants while improving surface finish and creating optimal profiles for coating adhesion.
1. Key Components & Working Principle
1.1 Major System Components
- Blast Chamber: Reinforced steel construction with replaceable liners
- Turbine Blast Wheels: High-speed (70-90 m/s) impellers with adjustable blade angles
- Hanger Conveyor System: Overhead chain conveyor with load-bearing capacity (typically 500-2000kg)
- Abrasive Recovery System: Vibratory screens + air wash separator
- Dust Collector: Multi-cyclone or cartridge filtration (99.9% efficiency)
1.2 Operational Workflow
- Workpiece loading on special hooks/fixtures
- Automated entry through labyrinth seals
- Multi-directional abrasive impact (2-4 blast wheels)
- Complete surface coverage via part rotation
- Abrasive recycling & debris removal
- Final inspection & unloading
2. Technical Specifications
ParameterTypical RangeChamber Size1.5-4m (L) × 2-3.5m (W) × 2-4m (H)Blast Wheel Power15-75 kW per wheelConveyor Speed0.5-3 m/min (variable)Abrasive Consumption5-20 kg per ton processedNoise Level≤85 dB(A) with sound insulation
3. Industrial Applications
- Automotive: Engine blocks, transmission cases
- Foundries: Castings deburring/descaling
- Aerospace: Turbine blade surface prep
- Railway: Wheel set cleaning
- General Engineering: Structural steel treatment
4. Maintenance Protocol
- Daily: Abrasive level check, dust collector inspection
- Weekly: Blast wheel wear measurement (max 20% loss)
- Monthly: Conveyor chain lubrication, liner thickness verification
- Annual: Complete system overhaul with bearing replacements
5. Safety Considerations
- OSHA-compliant emergency stop systems
- Interlocked access doors with pressure sensors
- Mandatory PPE: Respirators, hearing protection, blast suits
- NFPA-compliant fire prevention measures
6. Advantages Over Alternatives
- Higher throughput vs. manual blasting (up to 10 tons/hour)
- Consistent quality through automated parameters
- Lower labor costs with semi-automated operation
- Environmentally superior to chemical cleaning methods
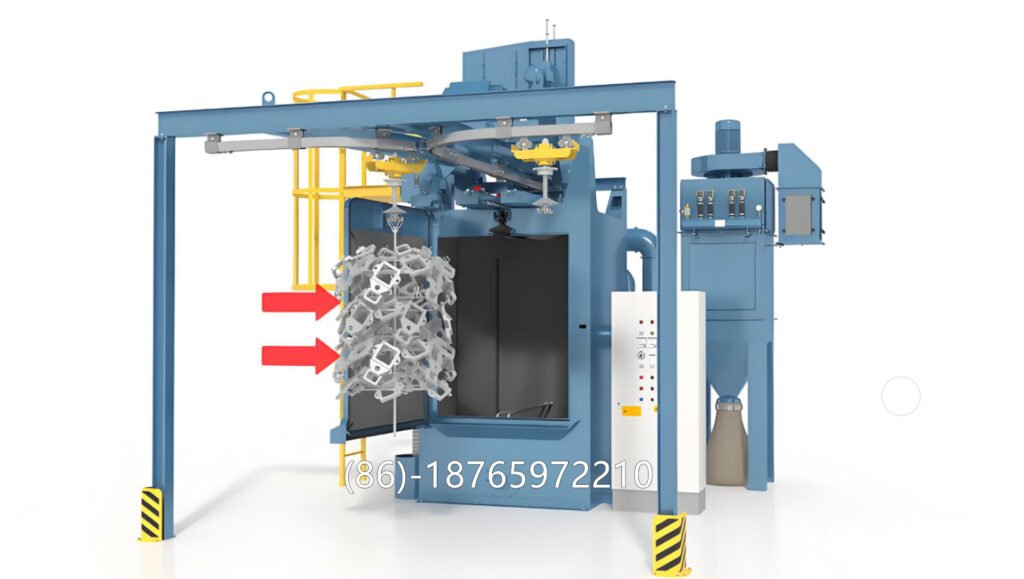
What is a Hanger Shot Blasting Machine?
A Hanger Shot Blasting Machine is a specialized, heavy-duty industrial system designed for the efficient and thorough surface treatment of components too large, heavy, or complex for manual blasting or tumblast systems. Think of it as a sophisticated “car wash” for industrial metal parts, but instead of soap and water, it uses high-speed abrasive particles propelled by centrifugal force to clean, descale, deburr, and prepare surfaces.
Core Principle:
Parts are hung (suspended) from hooks attached to an overhead conveyor system. They travel through an enclosed blast chamber where multiple high-powered turbines (blast wheels) propel abrasive media (steel shot, grit, cut wire) at high velocity onto all exposed surfaces. The rotation of the hooks ensures uniform coverage on complex geometries.
Why Use a Hanger Shot Blasting Machine?
- High Capacity & Productivity: Ideal for batch processing large volumes of heavy parts (frames, castings, forgings, fabricated structures).
- Large & Heavy Parts: Handles components too big or heavy for other automated methods like tumblers or conveyor belt systems (typical capacities 500kg – 5000kg per hook).
- Complex Geometries: The combination of multi-directional blasting and part rotation ensures thorough cleaning of intricate shapes, internal passages, recesses, and hard-to-reach areas.
- Consistent Quality: Automated control over blast time, wheel speed, abrasive flow, and conveyor speed ensures uniform and repeatable surface results.
- Improved Surface Properties: Removes rust, scale, oxides, sand, coatings & contaminants. Creates a clean, anchor profile essential for optimal paint/adhesive bonding.
- Deburring & Edge Rounding: Smooths sharp edges and removes burrs from machined or cut parts.
- Stress Induction: Can impart beneficial compressive stresses to improve fatigue life.
- Reduced Labor & Safer Operation: Significantly less manual handling compared to open blast rooms. Operators primarily load/unload outside the hazardous blasting environment.
- Abrasive Efficiency: Closed-loop recycling minimizes abrasive consumption and waste.
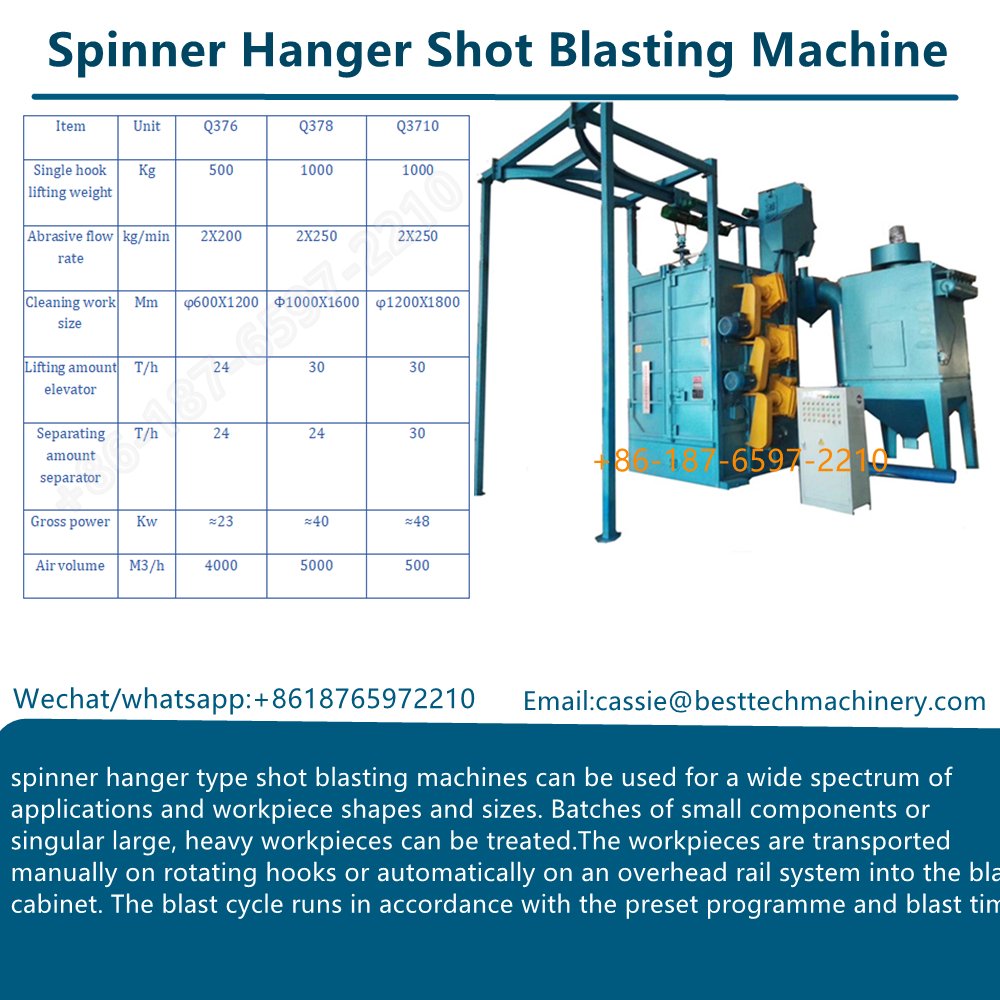
Types of Hanger Shot Blasting Machines
Hanger shot blasting machines are categorized based on design, automation level, and specialization. Understanding these variations is crucial for selecting the optimal system for specific industrial applications.
1. By Conveyor Configuration
- Single-Track Monorail System
- Design: Single overhead rail with hooks
- Capacity: 500-2,000 kg/hook
- Best For: Medium-weight components (engine blocks, gearboxes)
- Double-Track/Twin Monorail System
- Design: Parallel rails for simultaneous processing
- Capacity: 2,000-5,000 kg/hook
- Best For: Heavy fabrications (ship rudders, mining equipment)
- Continuous Loop System
- Design: Oval-shaped conveyor path
- Throughput: Up to 30 hooks/hour
- Best For: High-volume production (automotive foundries)
2. By Part Rotation Mechanism
Rotation Type | Mechanism | Precision | Applications |
---|---|---|---|
Free-Swing | Unpowered pendulum motion | Medium | Simple geometries |
Motorized Rotation | Electric gear-driven rotation | High | Complex impellers, turbine blades |
Programmable Axis | CNC-controlled multi-axis | Extreme | Aerospace components |
3. By Blast Chamber Design
- Standard Cabin Units
- Chamber Size: 2m(W)×2.5m(H)×4m(L)
- Blast Wheels: 2-4 turbines
- Typical Use: General manufacturing
- Tunnel Configuration
- Chamber Size: 3m(W)×4m(H)×10m(L)+
- Blast Wheels: 6-12+ turbines
- Typical Use: Shipbuilding, wind tower sections
- Modular Expandable Units
- Feature: Sectional bolt-together construction
- Advantage: Future capacity expansion
- Industries: Growing fabrication shops
4. By Automation Level
- Manual Loading Systems
- Operation: Operator places parts on hooks
- Cost Efficiency: Lowest initial investment
- Labor: Requires 1-2 operators
- Semi-Automated Cells
- Features: Automatic hook indexing + robotic part handling
- Cycle Time: 90-120 sec/loading sequence
- ROI: <18 months in high-volume plants
- Fully Automated Lines
- Integration: Connects to upstream casting/fabrication
- Technology: Vision-guided robotics + AI optimization
- Output: Up to 50 tons/hour
5. Specialized Variants
- Foundry Hanger Machines
- Unique Features: Heavy-duty sand separation, heat-resistant components
- Abrasive: Special cut wire for sand removal
- Temperature Tolerance: Up to 150°C
- Shot Peening-Specific Systems
- Control: Precision intensity gauging (Almen strips)
- Consistency: ±5% coverage uniformity
- Industries: Aerospace landing gear, springs
- Corrosion Removal Units
- Configuration: Extended dwell time chambers
- Media: Grit abrasives (G25-G80)
- Applications: Offshore platform structures
6. Industry-Specific Designs
- Automotive Hanger Systems
- Features: Quick-change fixtures, 45-sec cycle times
- Example: Dedicated engine block lines
- Aerospace Hanger Blasters
- Compliance: NADCAP-certified
- Precision: 0.5° rotation control
- Documentation: Automated traceability
- Rail-Specific Units
- Specialization: Bogie frame rotating cages
- Safety: ATEX-compliant dust extraction
- Capacity: 8,000 kg/hook systems
7. Loading Mechanism Comparison
Loading Type | Hook Design | Throughput | Limitations |
---|---|---|---|
Standard Hook | J-shaped steel | 10-15/hr | Simple parts only |
Fixture Plate | Custom bolted adapters | 8-12/hr | Dedicated tooling cost |
Inverted Pyramid | Multi-point suspension | 6-10/hr | Complex loading |
Robotic Gripper | Automated clamp systems | 20-25/hr | High capital investment |
Selection Hanger Shot Blasting Machine Considerations:
- Part Complexity: Multi-axis rotation required for internal passages
- Weight Distribution: Heavy asymmetric parts need balanced fixtures
- Surface Requirements: SA 2.5 (near-white metal) needs longer exposure
- Floor Space: Tunnel systems require >100m² area
- Abrasive Recovery: Wet blast systems for non-ferrous contamination
The optimal hanger shot blasting machine type depends on three critical factors: component characteristics (size/weight/complexity), required surface preparation standard (SSPC/SAE), and production volume. Modern systems increasingly incorporate IoT monitoring for abrasive consumption tracking and predictive maintenance, reducing operational costs by up to 40%. Always request material testing with your actual components before finalizing equipment selection.
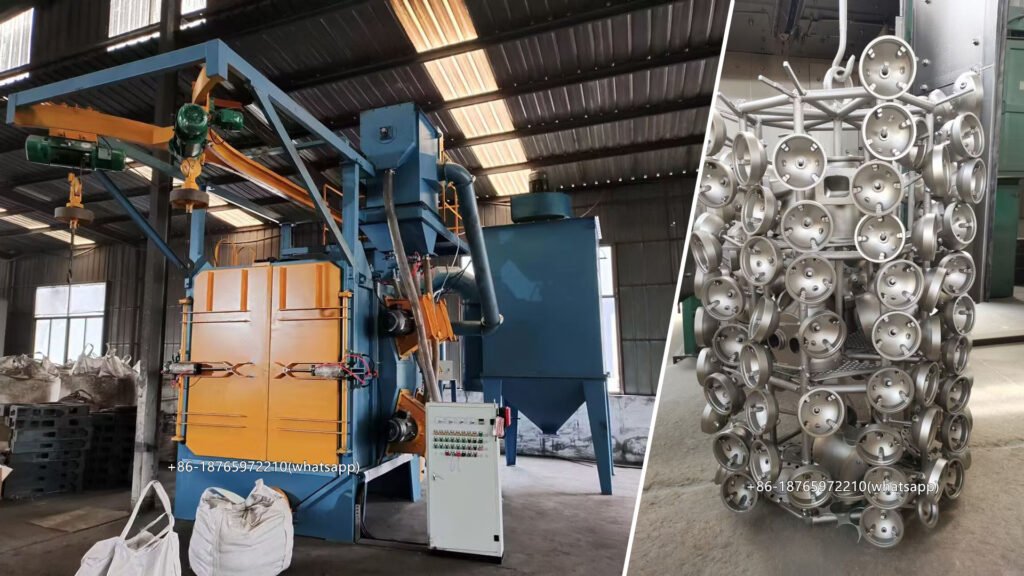
Precision Blasting Made Easy: How Hanger Shot Blasting Machines Guarantee Full Coverage Every Time
Modern surface treatment demands absolute consistency, and hanger shot blasting machines deliver this through engineered precision. These systems combine mechanical automation with physics principles to achieve complete coverage – even on complex geometries – with repeatable accuracy that manual methods can’t match.
1. The Coverage Challenge in Industrial Blasting
Surface preparation requires 100% abrasive impact – any missed areas compromise coating adhesion and corrosion resistance. Traditional methods struggle with:
- Shadow areas on complex parts
- Inconsistent manual operator techniques
- Varying blast angles on stationary systems
2. Engineering Solutions for Complete Coverage
2.1 Multi-Axis Part Manipulation
- Programmable Rotation: Electric rotators spin parts at 3-8 RPM during blasting (adjustable per part geometry)
- Oscillating Hooks: 15°-30° pendulum motion prevents “dead zones”
- Tilt Mechanisms: Optional 45° tilting for internal surfaces on hollow components
2.2 Strategic Blast Wheel Placement
- Angled Turbines: Wheels positioned at 25°/40°/55° for overlapping impact patterns
- Counter-Rotation: Adjacent wheels spin opposite directions to eliminate directional bias
- Variable Speed Control: 2000-3600 RPM adjustment for delicate vs. aggressive cleaning
2.3 Coverage Verification Systems
- High-Speed Imaging: CCD cameras validate coverage in real-time (95%+ detection accuracy)
- Almen Strip Testing: Standardized intensity measurement (SAE J442 compliant)
- Laser Profilometry: 3D surface mapping verifies anchor profile consistency
Conclusion
A Hanger Shot Blasting Machine is an essential piece of automated equipment for industries requiring high-volume, high-quality surface preparation of large, heavy, or complex components. By suspending parts on an overhead conveyor and subjecting them to controlled, multi-directional blasting within an enclosed chamber, it efficiently cleans, descaled, deburrs, and prepares surfaces for further finishing, ensuring consistency, productivity, and worker safety.