Still struggling with the mixing efficiency of greem sand?
Green sand, a critical material in sand casting processes, consists of silica sand, clay, water, and additives. Its uniformity and moisture balance directly impact the quality of castings, making efficient mixing a cornerstone of foundry operations.
High-speed green sand mixers have emerged as transformative tools, leveraging advanced engineering to optimize blending speed, consistency, and energy efficiency.
What is Green Sand?
Green sand is not actually green in color but refers to wet sand used in mold making. It is reusable and cost-effective, making it a preferred molding material for iron and non-ferrous foundries.
Typical composition:
85–95% Silica Sand
5–10% Bentonite Clay (binder)
2–4% Water
Additives (e.g., coal dust, dextrin)
The Development of Green and Sand Mixing: Innovations and Environmental Applications
The integration of green principles into sand mixing technology has become a critical focus in industrial manufacturing, particularly in foundry and construction sectors. This development aligns with global sustainability goals, emphasizing resource efficiency, reduced environmental impact, and circular economy practices.
Technological Innovations in Green Sand Mixing
Modern green sand mixing systems prioritize energy efficiency and material optimization. For instance:
High-Efficiency Sand Mixers: Advanced rotor-type sand mixers (e.g., S-series and GS models) combine low-speed scrapers with medium-speed rotors to enhance mixing capacity while minimizing energy consumption. These machines ensure uniform sand distribution and improved mechanical properties of the final product.
Recycled Materials Integration: The use of reclaimed foundry sand and additives like ammonium iodide-coated graphitic carbon nitride (NH4I@g-C3N4) reduces raw material waste and supports sustainable production cycles.
Environmental and Economic Benefits
Green sand mixing contributes to multiple sustainability objectives:
Reduced Carbon Footprint: Energy-efficient machinery and optimized processes lower greenhouse gas emissions, aligning with global decarbonization efforts.
Resource Conservation: Recycling sand and minimizing solvent use in chemical processes (e.g., mechanochemical synthesis) conserves natural resources and reduces landfill dependency.
Cost Efficiency: Long-term savings arise from reduced raw material costs and energy consumption, making green technologies economically viable for industries.
Challenges and Future Directions
Despite progress, challenges remain:
Regional Heterogeneity: The effectiveness of green policies and technologies varies by region, with central and eastern areas showing stronger adoption than western regions. Tailored strategies for underdeveloped regions are essential.
Material Compatibility: Ensuring recycled sand maintains structural integrity in high-precision applications requires further R&D.
Global Standardization: Harmonizing green manufacturing standards across industries (e.g., construction vs. foundry) will accelerate widespread adoption.
The evolution of green sand mixing reflects a broader shift toward sustainable industrial practices. By leveraging technological innovation, circular resource management, and collaborative policies, industries can achieve both ecological and economic resilience. Future research should focus on scalable solutions for small- and medium-sized enterprises, ensuring equitable access to green technologies.
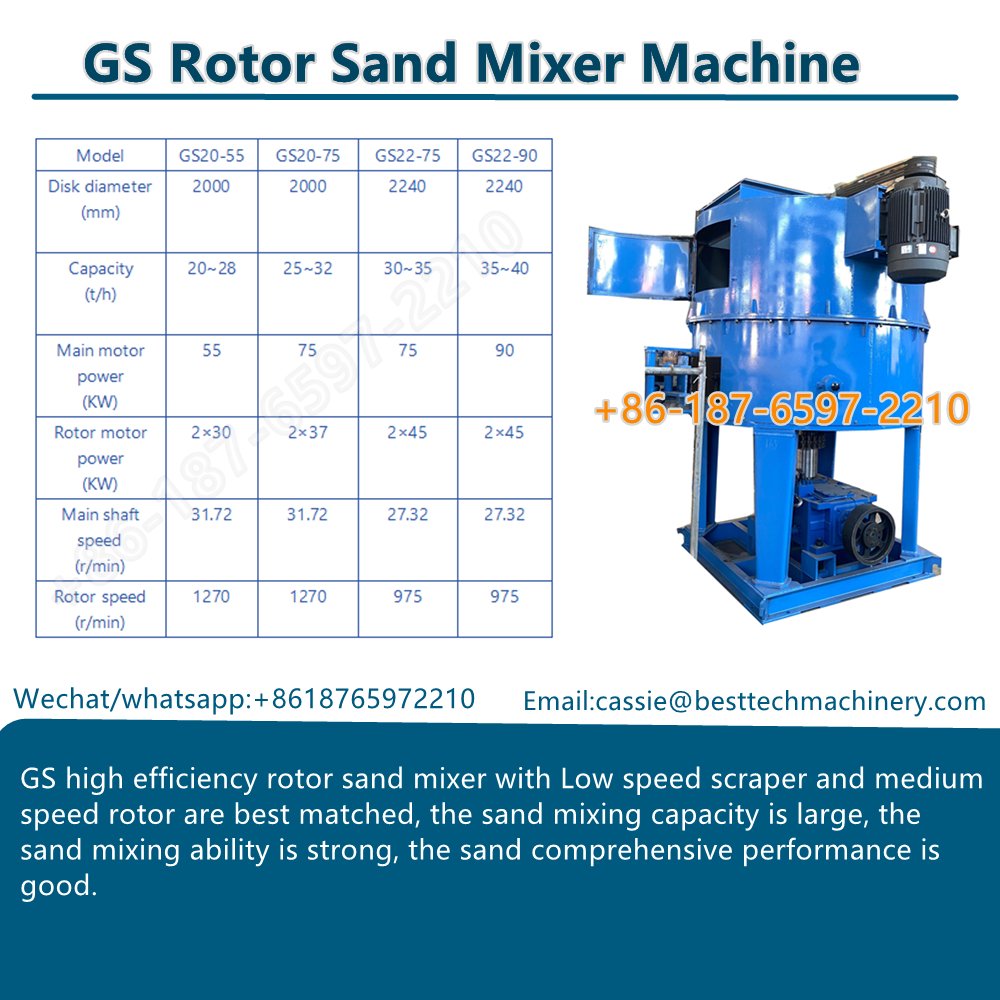
Introduction to Green Sand Mixing Technology
Green sand mixing represents a critical process in metal casting, where silica sand, bentonite clay (typically 5-10%), water (2-5%), and additives like coal dust or cereals are combined to create mold material. Modern high-speed mixers have evolved from traditional paddle mixers to sophisticated systems capable of producing perfectly homogeneous sand blends in 45-120 second cycles.
Technical Specifications Comparison
ParameterHigh-Speed MixerConventional MixerMixing Time45-90 sec120-300 secCapacity Range0.5-5 ton/batch0.3-3 ton/batchPower Consumption18-45 kW25-60 kWLifetime (cycles)500,000+200,000-300,000
Operational Benefits
- Production Efficiency:
- Enables 200-400 mold changes per shift
- Reduces sand-related casting defects by 60-80%
- Cost Savings:
- 15-20% lower binder consumption
- 30-40% reduction in sand waste
- Minimal maintenance requirements
- Smart Features:
- Self-diagnostic systems
- Predictive maintenance alerts
- Cloud-based recipe management
Selection Criteria for Foundries
- Evaluate hourly production requirements
- Consider sand system integration needs
- Assess available floor space (typical footprint: 15-30m²)
- Review automation compatibility with existing lines
- Calculate ROI based on labor/energy savings
Key Features & Benefits
Rapid & Uniform Mixing
High-speed rotors or impellers shear and mix the sand, binder, and moisture efficiently.
Ensures uniform binder and moisture distribution across the entire batch.
Short Cycle Times
High mixing efficiency allows fast batch or continuous mixing.
Increases mold production rate in high-throughput foundries.
Intelligent Control Systems
PLC/HMI integration for recipe-based mixing (moisture %, binder %, etc.).
Real-time monitoring and adjustments for sand temperature, moisture, and density.
Resource Efficiency
Lower binder and water consumption due to precision dosing.
Reduced energy usage per ton of sand processed.
Robust Construction
Wear-resistant liners and mixing elements extend machine lifespan.
Easy maintenance access to reduce downtime.
Popular Types of Green Sand Mixers
Type | Description |
---|---|
Batch Mixers | Mixes set quantities at a time; ideal for recipe control. |
Continuous Mixers | Ideal for large-scale operations with continuous mold lines. |
Rotor Type Mixers | Use high-speed rotors for fine dispersion of clay and water. |
Turbo Mixers | Advanced rotor-stator systems for very short mixing cycles. |
Summary
High-Speed Green Sand Mixing Machine is a specialized piece of foundry equipment used to efficiently mix green sand—a mixture of silica sand, clay (usually bentonite), water, and additives—used for making molds in metal casting. These machines are designed to ensure homogeneous mixing, short cycle times, and consistent mold quality in high-volume production environments.
Feature | Benefit |
---|---|
High-Speed Mixing | Shorter cycles, higher productivity |
Uniform Sand Quality | Better mold strength and surface finish |
Automation & Control | Consistent and repeatable performance |
Low Operating Cost | Reduced binder and energy consumption |
Durability | Long service life, low maintenance |