The Spinner Hanger Shot Blasting Machine is a highly versatile and efficient surface treatment solution widely used in foundries, automotive, aerospace, and metal fabrication industries. Designed for the cleaning, descaling, and surface preparation of a wide variety of workpieces, this machine provides excellent performance, especially for parts that are sensitive to impact or have complex geometries.
What is a Spinner Hanger Shot Blasting Machine?
A Spinner Hanger Shot Blasting Machine is a type of airless blasting system where workpieces are suspended from a rotating hanger. The parts are blasted by high-speed abrasive thrown from one or more blast wheels. During the blasting cycle, the hanger spins, ensuring that all surfaces of the workpieces are uniformly cleaned.
This machine typically operates in batch mode and is available in manual, semi-automatic, or fully automatic versions, depending on the level of productivity and integration desired.
Key Features
- Spinner Hanger System: Each workpiece is hung on a hook or hanger and rotated during blasting to ensure uniform surface treatment.
- Blast Wheels: High-performance blast turbines deliver abrasive media at high velocity for thorough cleaning.
- Compact and Enclosed Design: Prevents dust and abrasive leakage, ensuring operator safety and environmental protection.
- Customizable Layout: Available with single or double door design, Y-track, I-track, or continuous overhead conveyor systems.
- Wide Range of Applications: Suitable for castings, welded components, heat-treated parts, and components with complex shapes.
Advantages
- 360° Coverage: The rotating hanger ensures even blasting on all sides of the component, reducing blind spots.
- Damage-Free Cleaning: Ideal for delicate or thin-walled parts that may be damaged in more aggressive blasting systems like tumble or drum blasters.
- High Throughput: Multiple hooks or hangers allow continuous or semi-continuous operation for increased productivity.
- Easy Loading and Unloading: Parts can be loaded manually or with hoists/cranes, depending on machine design.
- Energy Efficiency: Efficient blast wheels reduce energy consumption while maintaining high cleaning performance.
Applications
- Foundry and Castings: Removal of sand, scale, and oxide from ferrous and non-ferrous castings.
- Welded Fabrications: Cleaning weld seams and preparing surfaces for painting or coating.
- Heat-Treated Components: Decarburization and oxide removal from heat-treated metal parts.
- Surface Preparation: Pre-treatment before painting, coating, or bonding to improve adhesion and longevity.
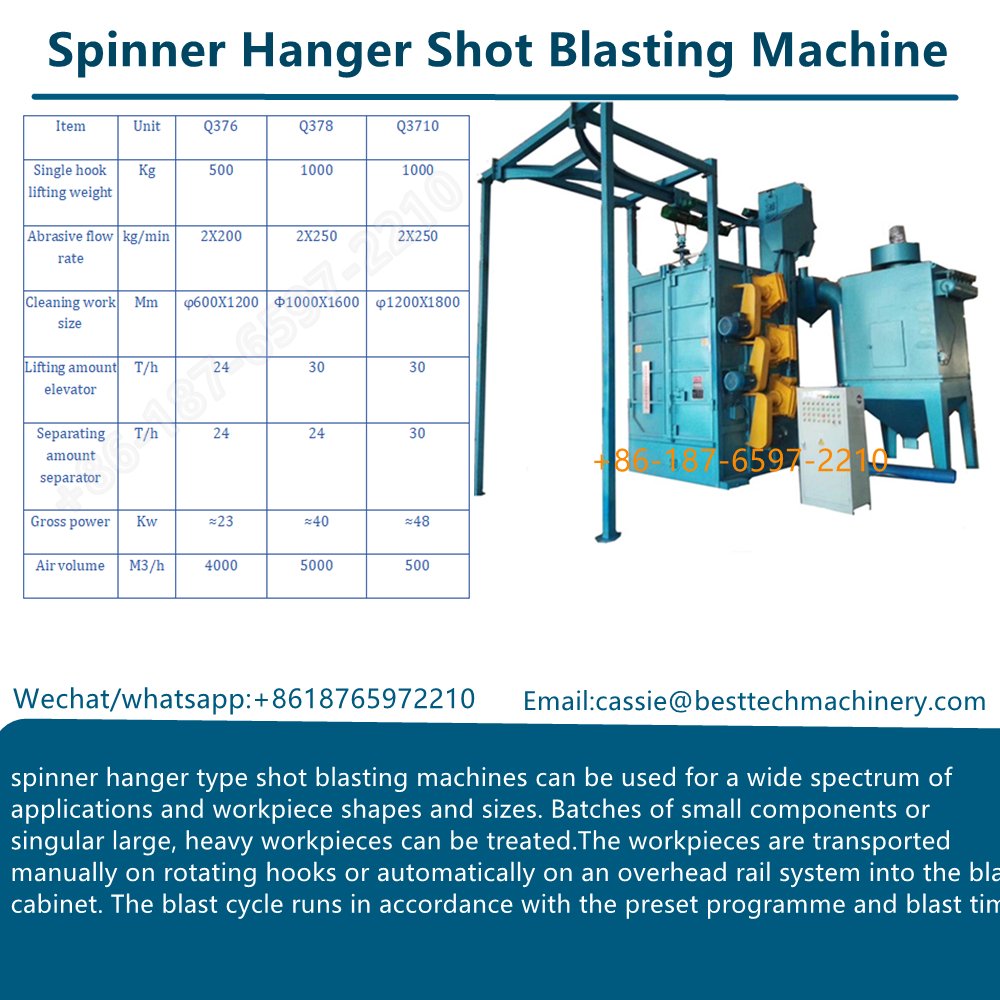
How to Choose the Right Spinner Hanger Shot Blasting Machine
1. Assess Your Workpiece Requirements
- Size and Weight: Measure maximum part dimensions (diameter, height) and weight
- Geometry: Evaluate part complexity (consider rotating capability for uniform coverage)
- Material: Different metals require specific blast media and intensities
- Surface Finish Requirements: Determine desired surface roughness (Ra values)
2. Production Capacity Needs
- Calculate required throughput (parts/hour)
- Consider future production growth
- Evaluate batch vs. continuous processing needs
3. Technical Specifications
- Spinner Configuration:
- Number of spindles (4-8 typical)
- Rotation speed range (20-75 RPM)
- Independent spindle control capability
- Blasting System:
- Turbine wheel size and quantity
- Blast media type and size compatibility
- Media recovery system efficiency
- Conveyor System:
- Load capacity per hanger
- Speed adjustment range
- Special fixturing requirements
4. Automation Level
- Manual loading vs. automatic integration
- Robot interface compatibility
- PLC control sophistication
- Data logging capabilities
5. Quality and Safety Features
- Dust collection efficiency (≥99%)
- Noise reduction technology
- Safety interlocks and emergency stops
- Wear monitoring systems
6. Vendor Evaluation
- Industry experience and references
- Service network availability
- Spare parts inventory
- Training and documentation quality
7. Cost Considerations
- Initial investment vs. lifecycle cost
- Energy consumption
- Maintenance requirements
- Media consumption rates
Selection Checklist
□ Workpiece size and weight capacity
□ Required surface finish quality
□ Production volume requirements
□ Available facility space
□ Future expansion possibilities
□ Maintenance accessibility
□ Environmental compliance
□ Operator safety features
Proper selection involves balancing technical requirements with budgetary constraints while considering long-term operational efficiency. Always request material testing and machine demonstrations before final purchase decisions.
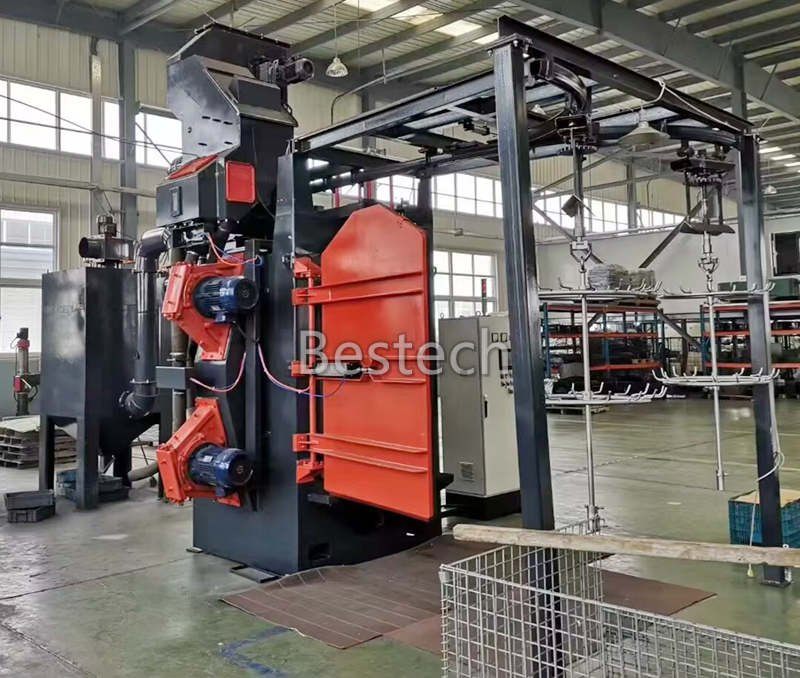
Why Choose Spinner Hanger Shot Blasting Machine?
Choosing a Spinner Hanger Shot Blasting Machine means investing in a high-quality, reliable system that combines thorough cleaning with gentle handling of your parts. It is especially advantageous when handling components with irregular shapes, fragile surfaces, or strict quality requirements. Its modular design also allows integration into existing production lines for enhanced automation and efficiency.
1. Exceptional Coverage on Complex Geometries
- 360-Degree Rotation: The spinning hangers rotate parts continuously during blasting, ensuring media reaches recesses, cavities, blind holes, and intricate contours impossible to treat uniformly in static or linear systems.
- Elimination of Shadow Zones: Consistent rotation prevents “shadowing,” guaranteeing complete coverage regardless of part shape.
2. Unmatched Process Consistency & Quality
- Uniform Surface Finish: Every surface receives equal exposure to the blast stream, resulting in consistent surface roughness (Ra/Sa values) and texture across all parts in a batch.
- Repeatable Results: Precise control over rotation speed, blast time, and media flow ensures identical treatment cycle after cycle, crucial for quality-critical industries like aerospace and automotive.
3. High Throughput & Productivity
- Continuous Operation: Parts move continuously through loading, blasting, and unloading zones on the overhead conveyor. Loading/unloading occurs simultaneously with blasting.
- Multi-Station Processing: Multiple spinner heads operate concurrently, allowing several parts to be blasted simultaneously within the same machine.
- Reduced Handling: Parts remain fixtured on hangers from loading through unloading, minimizing manual intervention and transfer time.
4. Optimized Efficiency & Cost Savings
- Reduced Media Consumption: Precise control and efficient blast patterns minimize media waste. Advanced recovery and recycling systems reclaim and reuse abrasives effectively.
- Lower Labor Costs: High automation reduces operator dependency compared to manual blast rooms or simpler machines.
- Reduced Energy Consumption: Efficient turbine designs and targeted blasting often consume less power per part processed than less sophisticated systems.
5. Enhanced Automation & Integration
- Inline Production: Seamlessly integrates into automated production lines (e.g., before painting, coating, or assembly). Parts enter and exit automatically.
- Robotic Integration: Compatible with robotic loading/unloading systems for fully automated, lights-out operation.
- PLC Control: Sophisticated control systems allow precise programming and monitoring of all parameters (speed, time, media flow, RPM).
6. Versatility Across Industries & Parts
- Wide Part Range: Ideal for components like engine blocks, cylinder heads, gears, shafts, turbines, pumps, valves, structural castings, forgings, and weldments.
- Industry Fit: Dominant in Automotive, Aerospace, Foundry (investment & sand casting), Oil & Gas, Heavy Machinery, and General Manufacturing.
- Multi-Purpose: Effectively handles cleaning (removing sand, scale, rust), descaling, deburring, surface preparation (for coatings), and stress relieving.
7. Improved Working Environment & Safety
- Contained Blasting: The enclosed cabinet design contains media and dust.
- Advanced Dust Collection: Integrated high-efficiency dust collectors (>99%) ensure a cleaner shop floor and protect worker health (meeting OSHA/MSHA standards).
- Reduced Noise Exposure: Sound-dampened enclosures significantly lower operational noise compared to open blasting.
- Safety Interlocks: Prevent door opening during operation and ensure safe shutdown sequences.
8. Superior Surface Preparation for Critical Applications
- Peening Capability: Achieves precise and consistent compressive stress profiles for critical fatigue-life components.
- Profile Control: Creates the ideal anchor pattern (SAE J444, SAE AMS 2430) for optimal coating adhesion.
- Stress Relieving: Effectively relieves stresses in machined or welded components.
When is a Spinner Hanger the RIGHT Choice?
Prioritize a spinner hanger machine if your requirements include:
- Complex-shaped parts needing all-around coverage.
- High-volume production demands.
- Consistent, high-quality surface finishes.
- Integration into automated manufacturing lines.
- Processing medium to large-sized components (typically 300mm – 1500mm diameter/width, 50kg – 500kg+).
- Industries with stringent quality and traceability standards.
Conclusion
Spinner hanger shot blasting machines offer a compelling combination of quality, productivity, versatility, and automation unmatched by simpler blasting methods. The investment is justified by their ability to deliver superior, consistent surface preparation on complex parts at high volumes, while optimizing operational costs and ensuring a safer workplace. For manufacturers seeking the pinnacle of efficiency and quality in their blast cleaning or surface preparation processes, the spinner hanger machine stands out as the technologically advanced solution.