Introduction to Tumble Shot Blasting Machine
Tumble shot blasting machines are specialized equipment designed for mass surface treatment of small to medium-sized metal parts. The process involves loading parts into a rotating barrel where they are continuously bombarded with metallic shots at high velocity. This mechanical action effectively removes surface contaminants while creating an ideal profile for subsequent coating or painting processes.
What Is a Tumble Belt Shot Blasting Machine?
Tumble shot blasting machine is an automatic abrasive cleaning system where workpieces are placed into a barrel- or drum-shaped chamber, which rotates or vibrates to tumble the parts. At the same time, high-speed abrasive media is projected onto the surfaces of the tumbling parts by a blast wheel. This simultaneous tumbling and blasting action ensures that all surfaces are evenly treated.
Key Features and Benefits
- High Efficiency: Capable of processing large batches simultaneously
- Uniform Treatment: Ensures consistent surface finish on all parts
- Versatility: Handles various part shapes and sizes (typically 5-150mm)
- Environmental Benefits: Closed-loop system minimizes dust emission
- Cost Reduction: Lower operational costs compared to manual methods
Working Principle
The machine operates through these stages:
- Parts loading into the rotating barrel
- High-velocity shot projection via turbine wheels
- Continuous tumbling action for even exposure
- Shot and part separation through vibration screens
- Clean parts discharge
Common Applications
- Automotive components (gears, springs, fasteners)
- Hardware and tool manufacturing
- Foundry operations (castings cleaning)
- Aerospace parts preparation
- General metal fabrication

How to Choose the Right Tumble Belt Shot Blasting Machine: Key Selection Factors
Selecting the optimal tumble belt shot blasting machine is critical for achieving efficient metal surface preparation, maximizing ROI, and ensuring long-term operational success. This guide outlines essential considerations:
1. Define Your Application Requirements:
- Part Characteristics: Size (min/max dimensions), weight, material (steel, aluminum, cast iron), geometry (complex shapes, thin walls), and initial surface condition (rust level, scale, coatings).
- Surface Finish Goals: Required cleanliness grade (Sa2.5, Sa3), desired anchor profile, surface roughness (Ra), or specific aesthetic finish.
- Process Objectives: Deburring, descaling, pre-paint/pre-coat preparation, stress relieving, or surface peening.
2. Evaluate Production Capacity:
- Batch Size & Weight: Maximum weight per batch the machine must accommodate.
- Throughput: Required kilograms/hour or batches/hour to meet production demands.
- Cycle Time: Target processing time per batch (influenced by part cleanliness needs and machine power).
3. Machine Configuration & Specifications:
- Barrel Size & Design: Internal volume/dimensions must allow parts to tumble freely. Consider liners (manganese steel, rubber, polyurethane) for wear resistance and noise reduction.
- Belt Discharge System: Belt width, speed, and durability. Ensure gentle part handling to prevent damage.
- Blasting Turbine(s): Number, size (wheel diameter), power (kW/HP), and placement. More/larger turbines increase intensity and coverage.
- Shot Velocity & Control: Adjustability is crucial for handling diverse parts and finishes.
- Shot Type & Size: Machine must be compatible with required shot media (steel grit, cut wire, ceramic beads – typically 0.2mm to 2.0mm). Include shot reclamation and classification system efficiency.
4. Blast Media & Separation:
- Shot Separation System: Vibratory screens, air wash, magnetic separators. Must efficiently separate shot from dust and part debris to maintain blast quality.
- Dust Collector: Adequate CFM capacity and filtration (cartridge filters recommended) to maintain visibility, ensure operator safety (air quality), and meet environmental regulations.
5. Automation & Control:
- Control System: User-friendly interface (HMI/PLC) for setting cycle times, barrel speed, belt speed, and monitoring operations.
- Loading/Unloading: Manual vs. automated options (hopper, conveyor feed) impact labor costs and throughput.
- Shot Addition: Automated shot replenishment systems enhance consistency.
6. Durability & Maintenance:
- Construction Quality: Robust welded steel frame.
- Wear Protection: Quality liners, turbine blades/blades, wear plates. Ease of replacement is vital.
- Accessibility: Design for easy maintenance access to turbines, screens, and critical components.
- Component Quality: Bearings, motors, gearboxes from reputable suppliers.
7. Space & Utility Requirements:
- Footprint: Physical dimensions and layout constraints in your facility.
- Power Supply: Required voltage (380V/415V/480V), phases, and amperage. Verify compatibility.
- Compressed Air: Requirements for controls/clamping (if applicable).
- Ventilation/Ducting: Space for dust collector placement and ductwork.
8. Safety & Compliance:
- Safety Features: Emergency stops, interlocks (door, access panels), guarding, safety light curtains.
- Noise Levels: Acoustic enclosures or linings may be necessary.
- Environmental Regulations: Dust emissions control (ensure collector meets local standards).
9. Supplier Evaluation:
- Experience & Reputation: Specialization in shot blasting equipment.
- Technical Support: Availability of installation, training, troubleshooting, and spare parts.
- References & Case Studies: Similar industry applications.
- Warranty & Service Agreements: Comprehensive coverage terms.
Comparative Decision Factors:
Factor | Lower Capacity/Small Parts | Higher Capacity/Large Parts |
---|---|---|
Barrel Size | Small (e.g., 300L) | Large (e.g., 1000L+) |
Turbines | 1-2 wheels, lower power | 2-4+ wheels, higher power |
Shot Media | Finer shot (0.2-0.6mm) | Coarser shot (0.8-1.5mm) |
Cycle Time | Shorter (3-8 mins) | Longer (8-20 mins) |
Automation Level | Often manual load/unload | Often automated feed/discharge |
Footprint | Compact | Significant |
Choosing the right tumble belt shot blasting machine requires balancing technical specifications, production needs, part specifics, and long-term operational costs. There is no universal solution. Carefully analyze your requirements, visit reputable manufacturers, witness machine demonstrations with your parts (or samples), and prioritize suppliers offering robust support. Investing in the correct machine ensures optimal surface quality, maximizes productivity, minimizes downtime, and delivers the best return on investment for your metal finishing operations.
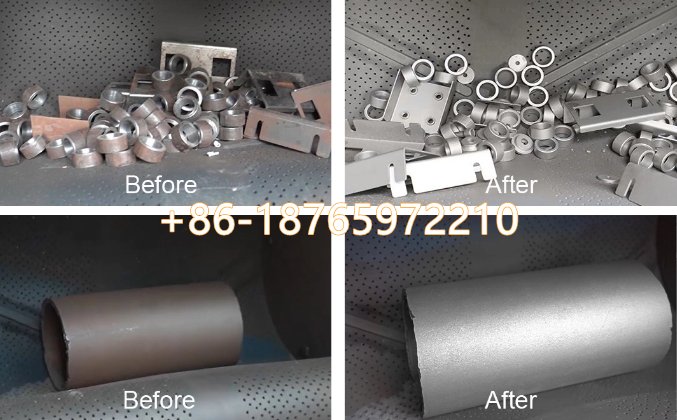
Why Choose Tumble Shot Blasting for Metal Surface Treatment?
1. Superior Cleaning Efficiency
- High-volume processing: Handles large batches simultaneously (typically 50-500kg per cycle)
- Time savings: Completes cleaning in 3-15 minutes per batch (vs. hours for manual methods)
- Automated operation: Continuous processing reduces labor requirements
2. Unmatched Surface Preparation Quality
- Consistent results: Uniform treatment of all part surfaces, including hard-to-reach areas
- Controlled intensity: Adjustable shot velocity (typically 50-90 m/s) for different requirements
- Optimal profile creation: Produces ideal anchor patterns (Ra 2-12μm) for coating adhesion
3. Versatile Material Handling
- Wide size range: Processes parts from 5mm to 150mm effectively
- Material compatibility: Works with steel, cast iron, aluminum, and other metals
- Shape adaptability: Handles complex geometries (gears, fasteners, castings) better than manual methods
4. Cost-Effective Operation
- Lower labor costs: Reduces manual cleaning workforce by 70-90%
- Media recycling: 95%+ shot reclamation rate minimizes consumable costs
- Energy efficiency: Modern designs consume 20-30% less power than older models
5. Environmental and Safety Benefits
- Closed-loop system: Contains 99% of particulates (vs. open blasting)
- Reduced waste: Proper shot separation extends media life
- Worker protection: Eliminates direct exposure to dust and noise
6. Process Advantages Over Alternatives
FeatureTumble BlastingManual CleaningVibratory FinishingConsistencyExcellentPoorGoodComplexity HandlingHighMediumLowThroughputVery HighLowMediumSurface Finish ControlPreciseVariableLimited
7. Industry Applications
- Automotive: Gear cleaning, engine components
- Aerospace: Turbine parts preparation
- Foundries: Casting cleaning and descaling
- General Manufacturing: Fasteners, hardware, tools
Conclusion
Tumble shot blasting machines deliver unmatched combination of speed, quality, and cost-efficiency for metal surface treatment. Their ability to handle diverse parts with consistent results makes them indispensable in modern manufacturing.