Jolt squeeze molding machine is a type of equipment used in foundries for creating sand molds in metal casting processes. It combines two actions — jolting and squeezing — to compact the molding sand around a pattern to form a mold cavity.
Jolt Squeeze Molding Machine Key Feature
- Jolt Squeeze Molding Machine is suitable for mass production of single moulding plate or single moulding box of medium and small-sized castings, which can produce cope or drag.
- Pneumatic components have a long service life and are convenient for operation, improving production efficiency.
- Optimized structure design. The square box frame structure significantly improves the rigidity of the machine body.
- The micro-vibration compaction process can significantly improve compaction strength and surface roughness to stabilize product quality. The hardness of sand moulding can reach above HB90.
- The shocking part is equipped with a buffer spring to effectively reduce the machine’s impact on the foundation.
- The pattern stripping mechanism adopts the cylinder, the crank, the connecting rod, and the synchronous shaft to realize the synchronous lifting.
- Fully adopt pneumatic parts to achieve the overall function of the control part, easy operation, and convenient maintenance.
How Jolt Squeeze Molding Machine Works
- Preparing the Pattern and Flask:
The pattern (a replica of the part to be cast) is placed on the pattern plate.
A flask (a box-like structure) is positioned around the pattern on the table of the machine.
Molding sand is poured into the flask and rammed to ensure it surrounds the pattern completely. - Jolting Action:
The machine’s table is lifted and then dropped repeatedly at high speed.
This jolting motion causes the sand to settle uniformly around the pattern, filling every crevice.
This step ensures the sand replicates the pattern details precisely and eliminates loose pockets in the sand. - Squeezing Action:
After jolting, the machine uses a squeeze head or plate to apply downward pressure on the sand.
This squeezing action compacts the sand further, ensuring uniform density and strength across the mold.
The squeezing pressure is adjustable based on the complexity and size of the mold. - Mold Removal:
Once the sand mold is fully compacted:
The squeeze head is retracted.
The mold is carefully removed from the pattern plate. In some cases, machines have mechanisms to lift the flask off the pattern gently.
The mold is then inspected for quality and any minor defects are fixed manually if needed. - Completing the Mold:
Additional steps like adding gating systems (for molten metal flow) or cores (for hollow sections in cast parts) are completed before assembling the mold halves.
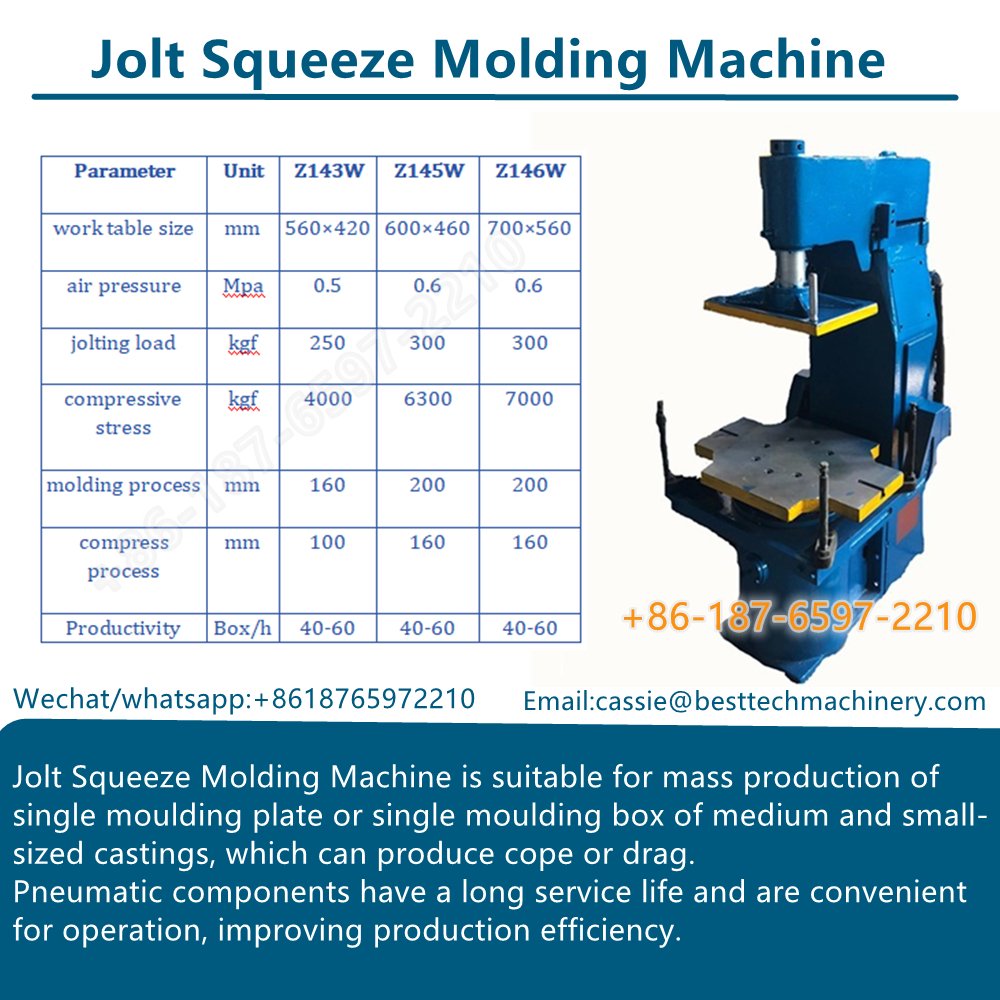
Jolt Squeeze Molding Machine Mechanisms
Jolt Mechanism:A pneumatic or hydraulic system powers the jolting motion.
The table is lifted and dropped repeatedly, guided by a controlled piston or cam system.
Squeeze Mechanism:A hydraulic cylinder or mechanical lever applies squeezing pressure.
The squeeze head presses evenly over the sand surface.
Advantages of the Jolt Squeeze Process
Precise reproduction of complex patterns.
Consistent mold density, reducing the risk of casting defects.
Faster mold production compared to manual methods.
Suitable for small to medium-sized foundries.
Jolt Squeeze Molding Machine Application
Jolt squeeze molding machine is widely used in foundries for various metal casting applications, especially for small to medium-sized components. Its primary purpose is to create strong, detailed sand molds for producing high-quality castings.
- Automotive Industry:
Engine components: Cylinder heads, crankcases, and manifolds.
Suspension parts: Control arms, brackets, and housings.
Transmission components: Gearbox casings and clutch housings. - Machinery and Equipment:
Agricultural machinery: Parts like pulleys, brackets, and housings.
Industrial machinery: Components for pumps, compressors, and turbines.
Power generation: Turbine blades, housings, and support structures. - Plumbing and Pipe Fittings:
Valve bodies, pipe joints, and flanges used in plumbing systems or industrial pipelines. - Construction Industry:
Building hardware: Hinges, brackets, and support structures.
Heavy equipment: Cast components for cranes, excavators, and bulldozers. - Aerospace and Defense:
Smaller components used in aircraft and defense systems where precise molds are necessary. - Electrical Industry:
Parts for motors, transformers, and electrical enclosures. - Tooling and Hardware:
Hand tools like wrenches, pliers, and machine tool bodies.
In summary, the jolt squeeze molding machine is ideal for creating durable sand molds in industries requiring precision, repeatability, and cost-efficient production of metal castings.